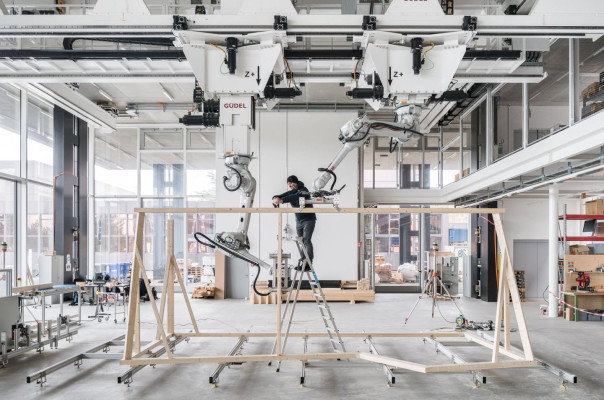

Being a neophyte in the world of woodworking — I’ve made a shabby but sturdy shed — I can appreciate the value of a good partner who can help measure, cut, hold stuff and generally be a second pair of hands. The usual drawback with humans is you have to pay them or feed them in return for this duty. So imagine my delight in finding that ETH Zürich is pioneering the art of robot-assisted woodworking!
The multi-institutional Spatial Timber Assemblies DFAB House project is an effort to increase the efficiency not just of the process of framing a home, but also of the design itself.
The robot part is as you might expect, though more easily said than created. A pair of ceiling-mounted robot arms in the work area pluck and cut beams to length, put them in position and drill holes where they will later be attached.
Most of this can be accomplished without any human intervention, and what’s more, without reinforcement plates or scaffolding. The designs of these modules (room-size variations that can be mixed and matched) are generated specifically to be essentially freestanding; load and rigidity are handled by the arrangement of beams.
The CAD work is done ahead of time and the robots follow the blueprint, carefully avoiding one another and working slowly but efficiently.
“If any change is made to the project overall, the computer model can be constantly adjusted to meet the new requirements,” explained Matthias Kohler, who heads the project, in an ETHZ news release. “This kind of integrated digital architecture is closing the gap between design, planning and execution.”
Human workers have to do the bolting step, but that step too seems like it could be automated; the robots may not have the sensors or tools available to undertake it at present.
Eventually the beams will also be reinforced by similarly prefabbed concrete posts and slot into a “smart slab,” optimized for exactly these layouts and created by sand-based 3D printing. The full three-story structure should be complete and open to explore this fall. You can learn more at the project’s website.